What is the Manufacturing Process for Glued Laminated Timber Beams?
Posted on 25-11-2024 11:41 AM
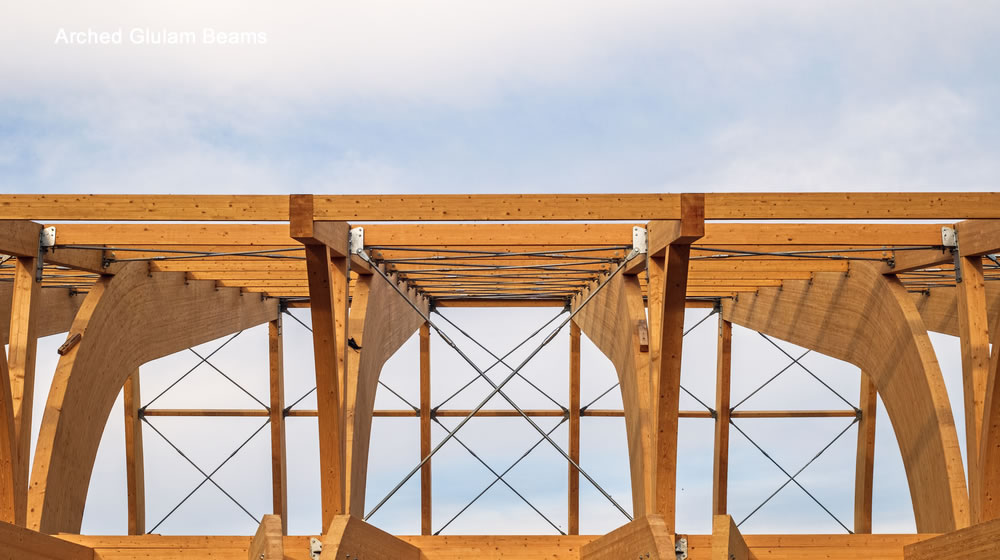
Glued laminated timber, often known as glulam, is a highly versatile and innovative construction material used for making large, strong structural beams. The manufacturing process of these beams is quite fascinating! It involves several steps that transform humble pieces of lumber into powerful structures capable of holding up buildings and bridges.
Firstly, the wood selection plays a critical role in determining the quality of the final product. Timber used for glulam is typically softwood species such as Spruce or Douglas Fir. However, hardwoods can also be utilized when needed (or desired). The chosen wood must be kiln-dried to achieve the correct moisture content; this step ensures stability and prevents future warping or twisting.
Once dried, workers inspect each piece of timber for imperfections like knots or cracks. They'll remove any defective sections because we don't want those weakening our beam! Next comes planing - where machines smooth out the surfaces to perfect uniformity. It's key that each lamella – that’s what we call the individual layers – fits snugly with its neighbors.
Here's where things get sticky - quite literally! We apply adhesives to one side of each lamella. Nowadays, manufacturers use incredibly strong, waterproof adhesives that meet stringent safety standards. This glue not only holds the lamellas together but also helps to transfer loads across them when they're under pressure in their final application.
Now it's time for lamination! Workers lay out all glued planks on top of one another (watching carefully to stagger any joints) and press them together using hydraulic presses. This isn't just a quick squeeze; these presses exert substantial force over an extended period - sometimes hours - ensuring every last drop of air escapes from between the layers and that adhesive penetrates deeply.
Once pressed and fully cured (which may take some more time), our beam almost looks like one solid piece of wood – but it ain't done yet! Craftsmen then shape it into its final form: this could be straight beams or curved ones depending on what architects have dreamt up (yes, we can curve wood!). Cutting-edge machinery controlled by computers ensures precision cuts so that everything fits just right during construction.
Before shipping out these architectural marvels, there’s quality control checks; after all, nobody wants a faulty beam supporting their roof! And finally (!), with all due care taken through each stage of production—voila—the glulam beams are ready to head off to construction sites around the world.
In summary, creating glulam requires careful treatment at every turn: from selecting suitable timber right down to packaging finished beams securely for transport. Each step demands attention (and perhaps a little patience). But boy oh boy—when you see those magnificent structures standing tall thanks to your handiwork... well now, doesn’t that just feel rewarding?